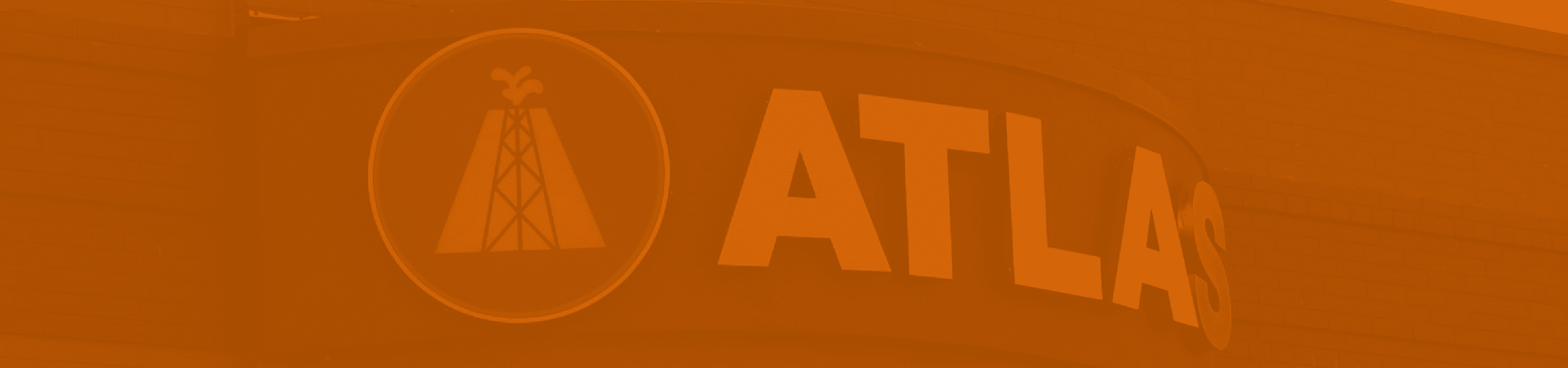
About Us
Headquartered in Houston, TX, Atlas Oil is the inaugural Simon Group Holdings company. Since our founding in 1985, Atlas has grown through technological and operational innovation, all while maintaining our unwavering commitment to customer success. Atlas offers single-source solutions for fuel, transportation and logistics and is one of the largest fuel distributors in the country, delivering over 1 billion gallons of fuel annually to customers in 49 states.
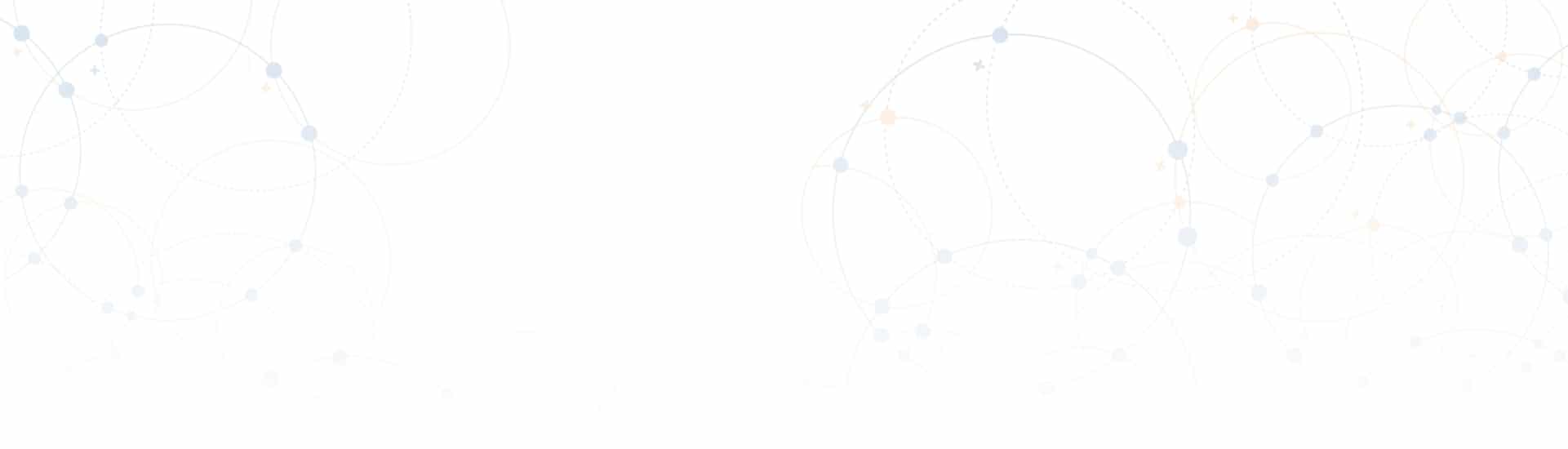
INNOVATING WITH FUEL DELIVERY
24/7 Service
We pride ourselves on having 24/7/365 live customer support to assist our customers with all their fueling needs.
Nationwide Partner
Delivery throughout the continental U.S. means you’ll have peace of mind with Atlas’ nationwide capabilities.
Atlas Advantage
We offer single-source solutions for your bulk liquid logistics and transportation’s needs.
LEARN MORE ABOUT US
THE HISTORY OF ATLAS OIL
Explore the key moments of innovation that define our rich history and unique identity.
CORE VALUES AND LEADERSHIP
Learn about the six core values we use daily to guide our actions and decisions.
CORPORATE LEADERSHIP
Get to know our company leaders and the pivotal roles they play in shaping our success.
GIVING BACK
THE SAM AND NADA SIMON FOUNDATION
The Sam and Nada Simon Foundation was established as the giving arm of Atlas Oil. The namesake of the Foundation and owners of Atlas Oil, Sam and Nada Simon, wanted a way to give back to the country that gave them their start and the opportunities to succeed after immigrating to the United States as teenagers. The Foundation’s core pillars of support include military (both active-duty and veterans), law enforcement and first responders, and education for disadvantaged youth.